Preventive/Corrective
WeContrL ensures the preventive and corrective maintenance required to keep your installation running well, to reduce the probability of failure or degradation. This maintenance includes :
- Periodic replacement of spare parts according to a predefined schedule
- Preventive maintenance and functional testing of the integrated equipment required for the aeraulic, electrical, mechanical and safety operation of the installation
- Verification, adjustment of set points and operating points to maintain performance at the validated level
- Verification, data collection, archiving, data analysis and reporting of operating parameters
- Advice on how to improve site operation, integrating an operating improvement approach
- Maintenance reports
Service available worldwide.
To be close to its customers, WeContrL has set up a network of experts on different continents
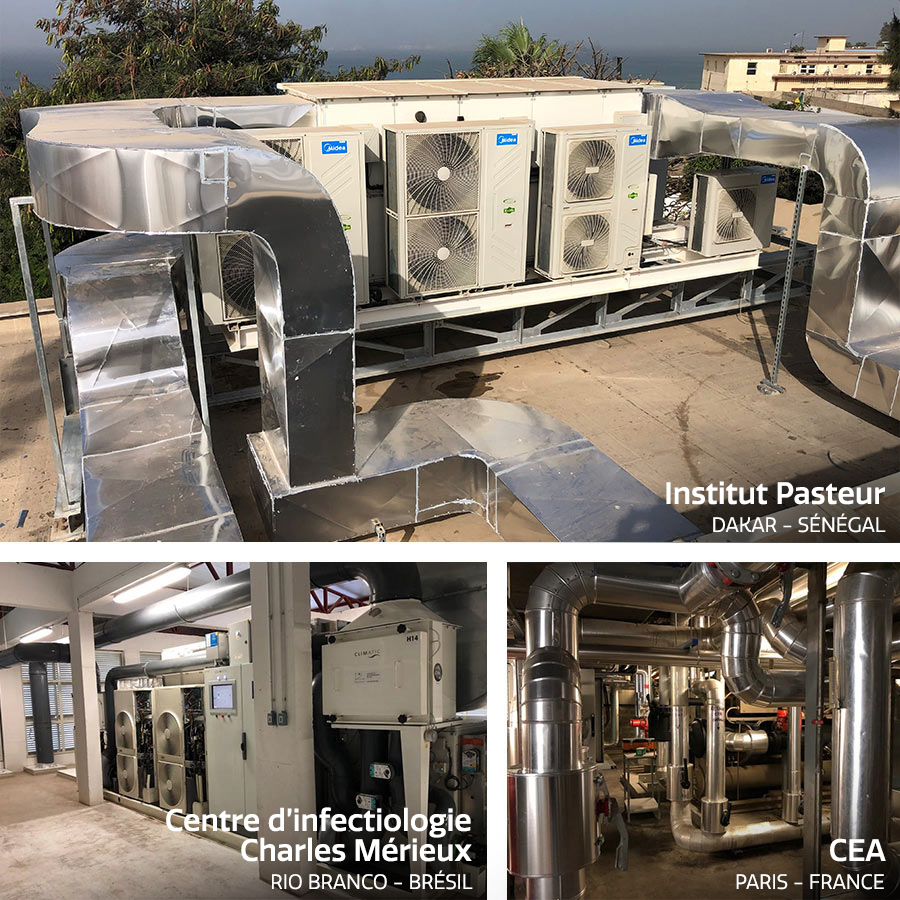
Remote maintenance contract
WeContrL undertakes, via remote connection, to monitor the correct operation of the equipment 24/7, thus guaranteeing the performance of your installation in any part of the world.
WeContrL will provide a monthly report on equipment performance and any malfunctions encountered during this period.
The customer can always monitor equipment performance using any device, including mobile phones, tablets and computers.
- 24/7 Hot Line
- A decision-support service is available every day for critical questions concerning system operation.
- Augmented reality glasses for assistance and support in maintenance processes.
Qualification
WeContrL offers qualification services (Equipment, Utilities, and HVAC) to guarantee the reliability of installations and compliance with ISO 14644-1 and 3 standards.
In addition to general preventive maintenance, this qualification involves checking:
- The cleanliness class of the confined environment
- Integrity of filters where necessary
- Temperature/pressure/flow rate compliance
- General operation of the system and all accessories, with particular attention to safety features
OQ, IQ (Operational Qualification, Installation Qualification) tests can be carried out.
Installation Qualification = Verification of the conformity of the characteristics of the equipment delivered, its installation and operation in the "start-up" phase.
Operational Qualification = Verification of equipment functionality and performance, in accordance with manufacturer's recommendations.
FAT (Factory Acceptance Test): acceptance tests at the supplier's, carried out before shipment to minimize the occurrence of malfunctions during the start-up process.
SAT (Site Acceptance Test): acceptance tests carried out on the customer's site after delivery, to check that the equipment has arrived correctly, and that the system is operating correctly before commissioning.
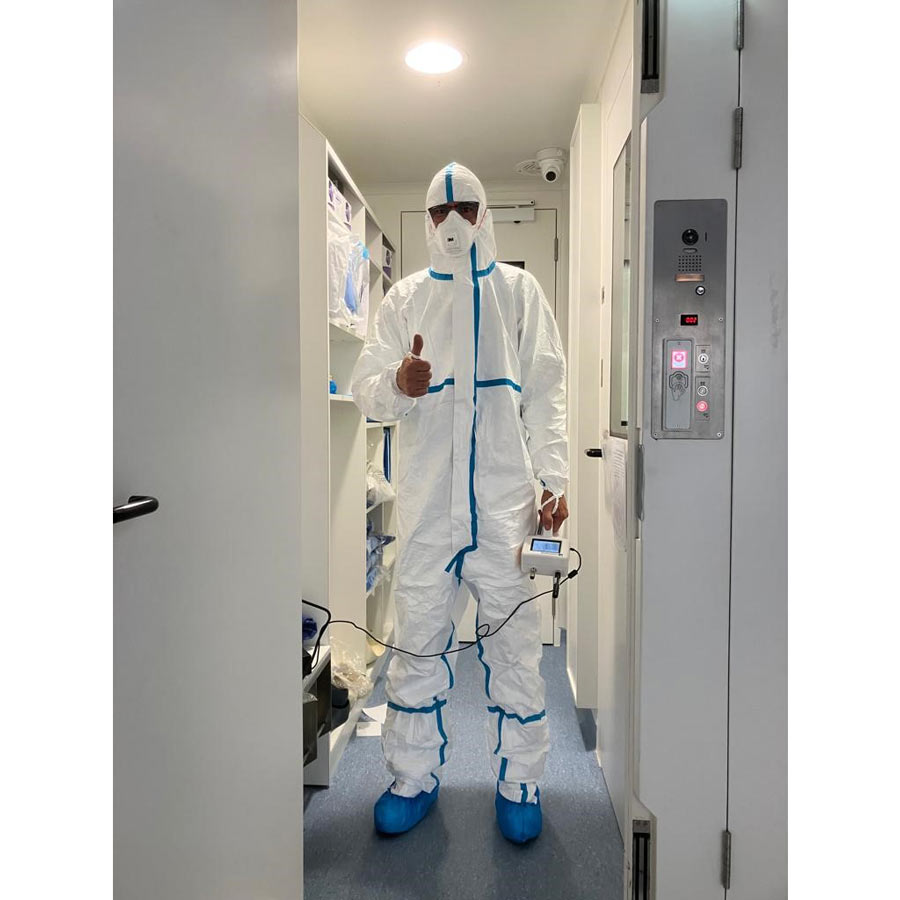